Furthermore,heat transfer-inducedenergyhomeowners.Moreover,energybarrierheatclimate,polyurethane foamfeasible.Conversely,energyspray foam,investmentbudgetenergycost-effectivewall situation.
Are you grappling with the decision of how to insulate your attic and concerned about the costs involved? This article will dissect the expenses associated with spray foam and traditional insulation materials like fiberglass and cellulose. We’ll delve into the factors that sway the overall cost, including the wall ‘s role in heat transfer, and provide a comparative analysis of long-term savings. By understanding these costs, you’ll be equipped to make an informed choice that not only suits your budget but also enhances your home’s resistance to heat loss.
Understanding Different Types of Attic Insulation
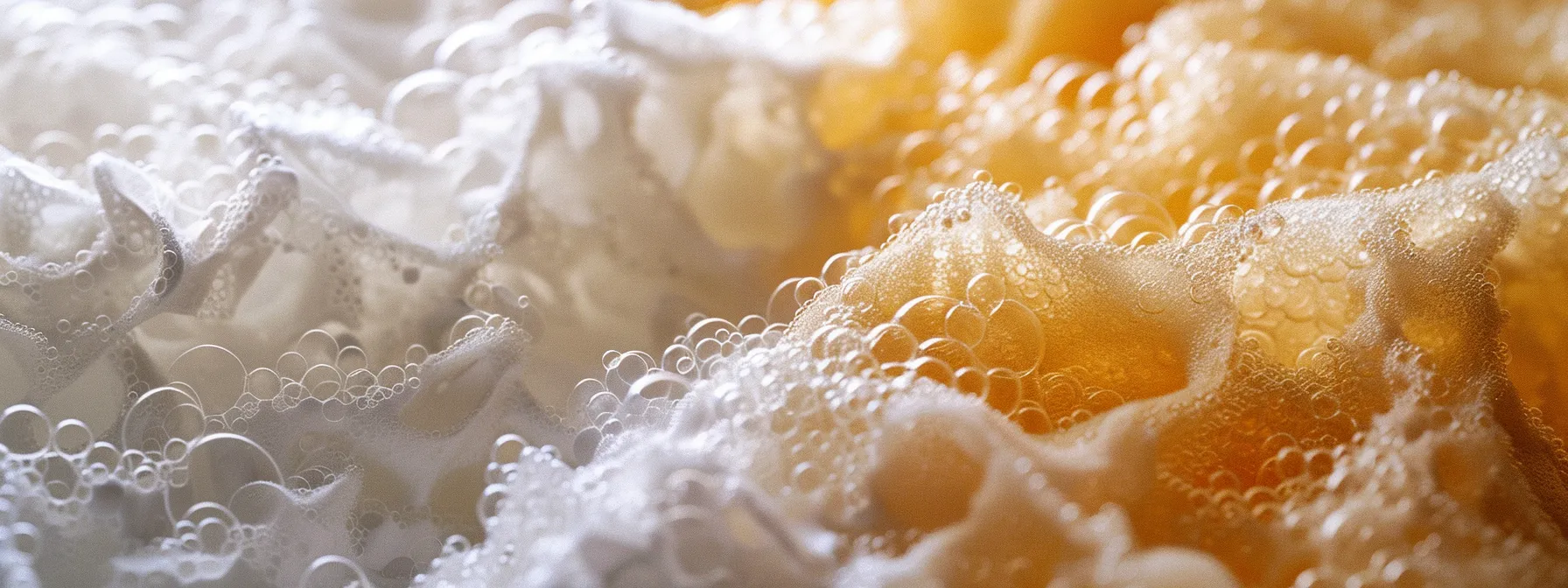
As we examine the costs of attic insulation, it’s crucial to understand the various options available. Spray foam insulation offers a modern approach, sealing nooks and crannies to prevent ice dams and water intrusion. Traditional materials, such as fiberglass and cellulose, provide time-tested solutions that insulate wood structures from temperature extremes. We’ll compare their R-values to determine efficiency, consider the environmental impact of our choices, and address health and safety concerns, especially around the eaves. This comparison will guide us in making informed decisions for our homes.
Overview of Spray Foam Insulation
When I consider the insulation of a house, spray foam stands out as a robust investment for long-term energy savings. Unlike traditional materials, spray foam attic insulation expands to fill gaps, providing an airtight seal that significantly reduces the risk of ice dam formation. Its superior R-value, often reaching up to R60 insulation, ensures that heat stays where it’s intended, leading to a more consistent indoor climate and lower utility bills. Roof
My experience with spray foam has shown it to be particularly effective in preventing ice dam intrusion, a common concern in attic spaces. By creating a seamless barrier, it not only insulates but also fortifies the house against water damage. This dual action makes spray foam attic insulation a wise choice for those looking to enhance their home’s energy efficiency and protect their investment from the elements.
Overview of Traditional Insulation Materials
In my professional experience, traditional insulation materials like fiberglass and cellulose are widely recognized for their cost-effectiveness and compliance with building codes across the United States. Homeowners often search for”blown in insulation near me” to find services that can install these building insulation materials, which can be less expensive upfront compared to spray foam. These options are particularly appealing for those looking to improve their furnace‘s efficiency through better attic insulation, ultimately contributing to energy conservation and reduced heating costs.
Having worked with various insulation types, I’ve observed that traditional materials, while not as airtight as spray foam, still play a significant role in maintaining a home’s wall temperature. They are often preferred in retrofit situations where the existing structure may not support the density of spray foam. Moreover, these materials meet the essential requirements for attic insulation, helping homeowners in colder climates keep their homes warm without overburdening their furnaces, thus aligning with energy conservation goals.
Comparing R-Values and Efficiency
In my role as a point of sales expert, I’ve seen how home improvement projects, particularly those involving attic insulation, can significantly impact a home’s energy efficiency. When comparing R-values, which measure thermal resistance, spray foam often outperforms traditional materials like fiberglass or glass wool. For instance, while standard fiberglass insulation might have an R-value ranging from R-2.9 to R-3.8 per inch, closed-cell spray foam can reach R-6.5 to R-7 per inch. This higher R-value means better insulation per inch of thickness, leading to enhanced temperature control in every room and potentially lower heating and cooling costs for the homeowner.
Moreover, I’ve observed that in areas with high humidity, the choice of insulation can affect not just the room temperature but also the overall indoor air quality. Spray foam’s ability to create a moisture barrier can help prevent the growth of mold and mildew, which is crucial for maintaining a healthy living environment. On the other hand, traditional materials like glass wool can absorb moisture, which may compromise their insulating properties and affect the structural integrity of the ceiling over time. Therefore, it’s essential for homeowners to consider both R-values and the specific conditions of their attic space when selecting polyurethane insulation materials.
Environmental Impact of Insulation Choices
When I advise clients on the best insulation for attic spaces, environmental considerations are paramount. Spray foam insulation, while effective in sealing spaces and preventing mold, often contains chemicals that may raise concerns about its ecological footprint. On the other hand, materials like cellulose insulation are made from recycled paper, which is less harmful to the environment and can be an eco-friendlier option for insulating between roof joists and throughout the attic space.
In my experience, homeowners are increasingly conscious of their choices’ impact on the environment. For those looking to minimize their carbon footprint, selecting the best insulation for attic areas involves a careful balance between performance and sustainability. Products like fiberglass that contain a high percentage of recycled glass can offer a compromise, providing effective insulation while also being kinder to the planet. It’s crucial to consider both the immediate and long-term effects of building insulation materials on the environment when making decisions for your home.
Health and Safety Considerations
In my professional dealings, I’ve observed that the installation of building insulation must prioritize health and safety. For instance, when using fiberglass, it’s imperative to have a proper pump system for installation to minimize airborne particles, which can irritate the respiratory system. Additionally, ensuring that a vapor barrier is in place is crucial to prevent moisture accumulation, which can lead to mold growth and compromise indoor air quality.
When I advise clients on insulation, I emphasize the importance of considering the knee wall areas, which are often overlooked. Cellulose, being a denser material, can provide excellent floor soundproofing and temperature regulation without the potential chemical sensitivities associated with spray foam. It’s essential to weigh these health and safety factors carefully, as they directly impact the well-being of the occupants and the overall efficacy of the insulation over time.
Cost Breakdown of Spray Foam Insulation
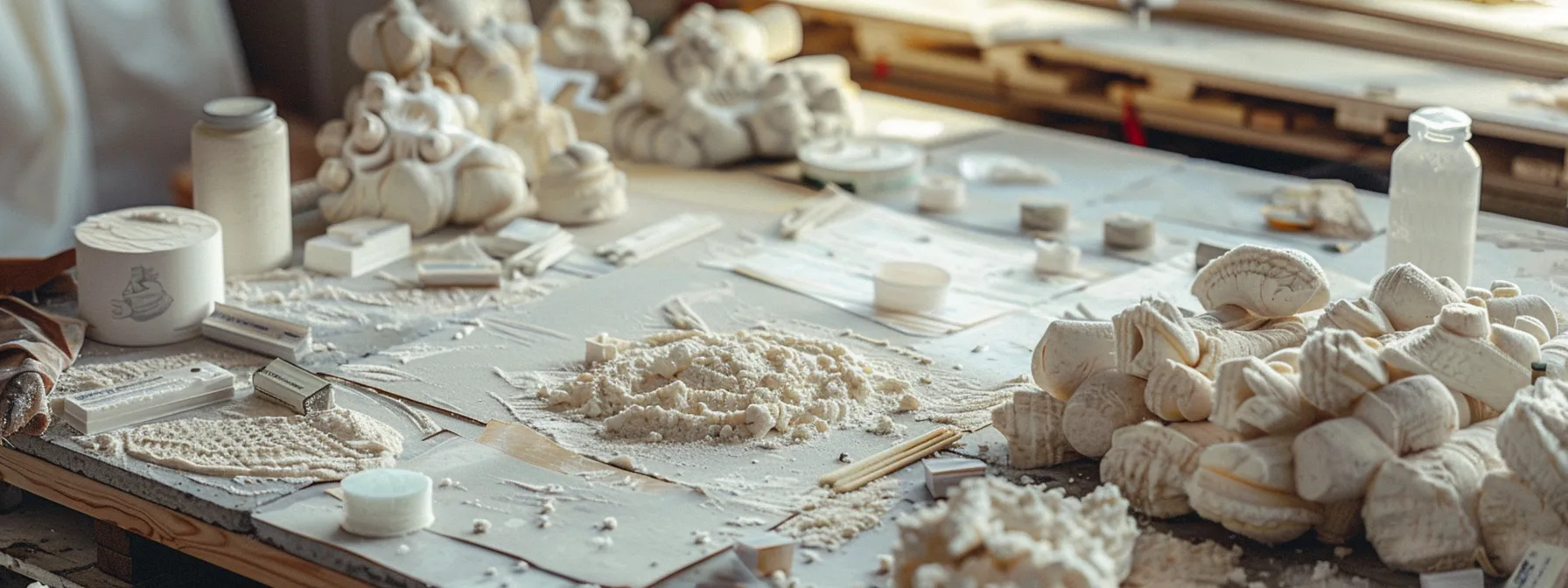
Delving into the financial aspects of spray foam insulation, I’ll break down the material costs, including the price for blown-in insulation, and the expenses tied to its installation. We’ll examine the long-term maintenance and durability of this high-density solution, alongside the energy savings potential it offers. Through case studies, we’ll assess the cost efficiency of spray foam compared to mineral wool insulation and other traditional materials, providing you with a comprehensive understanding of your investment.
Material Costs for Spray Foam
When I guide clients through the intricacies of spray foam insulation costs, I emphasize the importance of a thorough inspection. The initial outlay for spray foam is typically higher than traditional fiber materials, reflecting its advanced technology and labor-intensive application. An energy audit often reveals that despite the steeper price, the long-term savings on heating and cooling can be substantial, particularly when sealing complex roofing and ceiling structures.
My experience has shown that while the material costs for spray foam are considerable, they must be evaluated alongside potential plumbing and electrical modifications. Unlike fiberglass, spray foam‘s expansive nature can complicate access to these systems, necessitating careful planning and possible additional expenses. However, the investment can enhance the overall energy efficiency of a building insulation , leading to reduced utility bills and a more comfortable living environment.
Installation Expenses for Spray Foam Insulation
In my professional capacity, I’ve observed that the installation expenses for polyurethane insulation are influenced by the complexity of the construction and the need for skilled labor. The process requires meticulous attention to detail, particularly around wall cavities and ventilation areas, to ensure proper airflow and prevent thermal bridging. This precision, while it may increase initial costs, is vital for maximizing the efficiency of attic hatch insulation and the overall energy performance of the home.
Moreover, I’ve advised clients that the cost of installing spray foam insulation can be affected by the existing state of the attic. If modifications to enhance ventilation or repair damages are necessary, these will add to the overall expense. However, the investment in creating a well-sealed and insulated attic space pays dividends in the form of reduced energy bills and a more comfortable indoor climate, particularly in areas where temperature fluctuations are significant. The wall will also affect the energy conservation
Long-Term Maintenance and Durability
In my professional experience, the durability of spray foam insulation is one of its most compelling advantages. Unlike zonolite insulation, which may degrade over time or require retrofitting, spray foam maintains its integrity, reducing the need for removing insulation from the attic. This stability ensures that air conditioning systems operate more efficiently, as the insulation continues to provide a high level of thermal resistance without significant settling or deterioration.
when I assist clients with their insulation choices, I often highlight that spray foam‘s resilience means fewer maintenance demands. Pipes and ductwork insulated with spray foam are less likely to suffer from
stress, minimizing the risk of cracks or leaks. This long-term reliability not only protects the home’s structure but also translates into sustained
savings and comfort for
Energy Savings Potential With Spray Foam
From my experience, the energy savings potential with spray foam insulation is substantial, particularly when integrated into a comprehensive building insulation strategy. By creating an impermeable barrier, spray foam minimizes the energy loss typically associated with traditional materials, allowing heat pumps and HVAC systems to operate more efficiently. This efficiency is evident in homes where spray foam has been applied to drywall, glass, and framing junctions, areas notorious for energy leakage.
Moreover, clients have reported a noticeable decrease in their energy bills after retrofitting their attics with spray foam insulation. The material’s ability to maintain a consistent temperature reduces the strain on heating and cooling systems, leading to long-term cost savings. In my role, I’ve seen firsthand how spray foam‘s superior insulating properties contribute to a more energy-efficient home, affirming its value as a smart investment in building insulation using polyurethane.
Case Studies on Spray Foam Cost Efficiency
In a recent project I oversaw, the installation of polyurethane insulation in the rafters of a flat roof led to a marked improvement in thermal efficiency. The homeowner, initially concerned about the cost, was pleased to find that the energy savings began to offset the initial investment within the first year. This case exemplifies how the higher R-value per inch of polyurethane can lead to significant long-term savings, especially in homes with unique architectural features that are challenging to insulate with traditional materials.
Another case involved a basement renovation where blown in wall insulation was considered, but polyurethane was chosen for its moisture-resistant properties. The client reported not only a warmer basement in the winter months but also a reduction in external noise, an unexpected but welcome benefit. This experience underscores the multifaceted value of polyurethane insulation, which extends beyond energy savings to enhance comfort and livability in areas of the home that traditional insulation might not adequately address.
Cost Breakdown of Traditional Insulation Materials
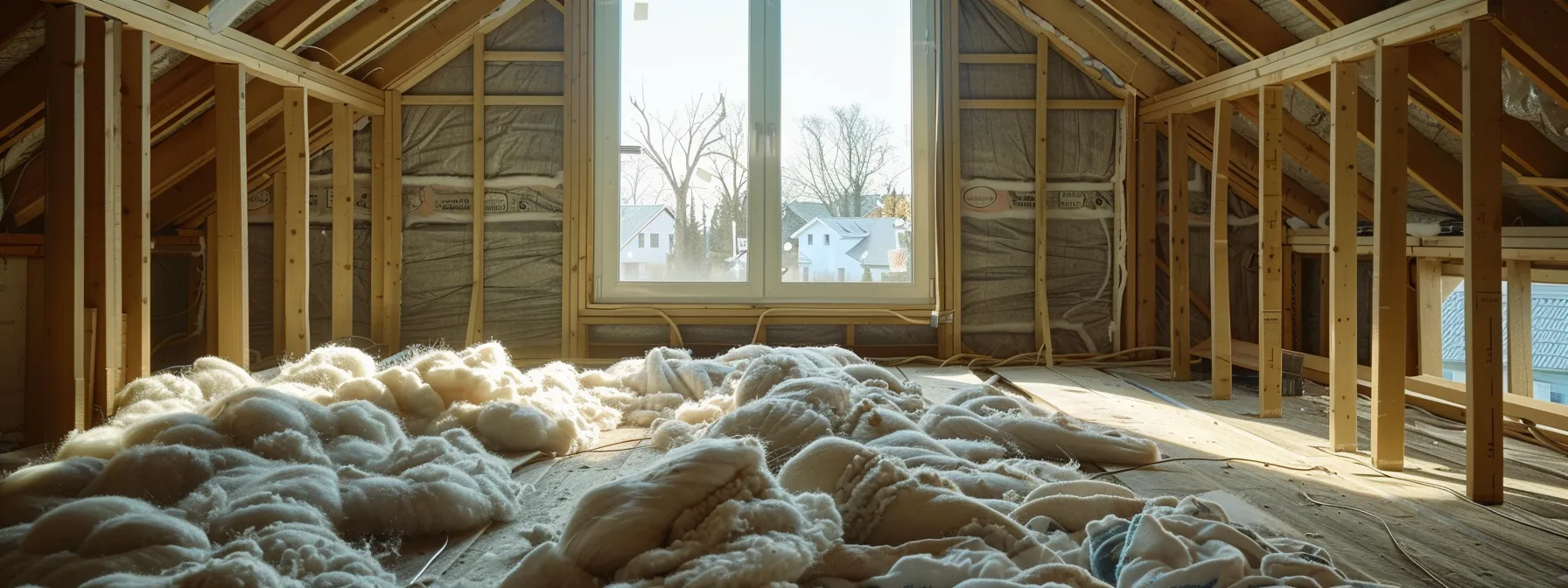
Turning our attention to traditional insulation materials, we’ll delve into the specifics of fiberglass and cellulose, including their material costs and the expenses associated with installation. I’ll share insights on the maintenance requirements and lifespan of these options, as well as the energy savings they can offer. Through case studies, we’ll evaluate the cost efficiency of these materials, considering factors like soundproofing capabilities and their performance in various climates, including crawl spaces. This analysis will also touch on the broader implications of our choices in the context of climate change, contrasting these materials with spray foam insulation.
Material Costs for Fiberglass and Cellulose
In my professional dealings, I’ve found that the material costs for fiberglass and cellulose insulation are generally more budget-friendly than spray foam, making them a viable option for those undergoing a renovation with financial constraints. Fiberglass, a mineral-based barrier, is particularly cost-effective and can be easily fitted around electrical wiring, which is a common challenge in attic spaces. Cellulose, while slightly more expensive than fiberglass, offers a higher R-value and is often treated to be fire retardant, adding an extra layer of safety to a building insulation .
During a recent project, I advised a client who was looking to take advantage of the Enbridge Home Efficiency Rebate program. We opted for cellulose insulation, which not only met the program’s requirements but also provided a substantial thermal barrier in their attic renovation. This choice resulted in both immediate cost savings on materials and a long-term reduction in energy bills, demonstrating the practical and financial benefits of selecting traditional building insulation materials in certain scenarios.
Installation Expenses for Traditional Insulation
In my experience, the installation expenses for traditional insulation like mineral wool or fiberglass are often more manageable for many of my clients. The blown in insulation cost, for instance, is typically calculated by the square footage and depth of the insulation required, making it easier to estimate and budget for. I’ve found that the use of polyethylene as a vapor barrier in conjunction with these materials can also affect the overall cost, but it’s a necessary addition to ensure moisture control and longevity of the insulation.
When I work with clients, I take precise measurements of their attic space to determine the quantity of insulation needed, which directly influences the cost. Unlike spray foam, which is a liquid application, traditional materials like mineral wool come in batts or can be blown in, offering a cost-effective solution without the need for specialized equipment. This simplicity in installation not only helps in keeping the costs down but also allows for a quicker turnaround, minimizing disruption to the household.
Maintenance Requirements and Lifespan
In my professional experience, traditional insulation materials like fiberglass and cellulose, while cost-effective, do require periodic checks to ensure they maintain their integrity over time. The trusses and dams in your attic can be particularly vulnerable to the long-term effects of moisture, which can compromise the effectiveness of these materials. Regular inspections can help identify any need for additional polyurethane sealing to reinforce the air barrier and maintain the insulation’s performance.
Furthermore, I’ve observed that the lifespan of traditional foam insulation can be extensive, provided it’s installed correctly and with adequate ventilation. Over time, however, it may settle or compact, reducing its original R-value and necessitating top-ups or replacement to sustain its thermal resistance. Homeowners should be prepared for this maintenance aspect to ensure their attic continues to serve as an efficient air barrier against temperature extremes.
Energy Savings With Traditional Materials
In my professional experience, traditional materials like polystyrene and fiberglass can offer significant building insulation savings, especially when installed correctly around ductwork to prevent condensation and energy loss. These materials, while on a budget, can effectively reduce heat transfer, maintaining a comfortable temperature in the living spaces below. Homeowners who prioritize cost-effectiveness often find that these solutions meet their needs without compromising on performance.
I’ve advised clients on the strategic placement of insulation to avoid common issues like the overheating of recessed lights, which can be a fire hazard and also a source of
inefficiency. By choosing the right materials and ensuring proper installation, traditional insulation can provide a reliable
against
loss, contributing to lower utility bills and a more consistent indoor
even in older homes where upgrading to
might not be
Case Studies on Traditional Insulation Cost Efficiency
In a recent consultation, I advised a retail store owner who was combating high energy bills due to freezing drafts entering through the soffit. We decided on loose fill cellulose insulation, which proved to be a cost-efficient solution. Not only did it significantly reduce the store’s heating costs, but the owner also noticed a remarkable decrease in street noise, enhancing the shopping experience for customers.
Another case involved a homeowner who was experiencing uneven temperatures throughout their residence. After inspecting their attic, I recommended adding additional layers of fiberglass batt insulation. This relatively low-cost intervention led to a marked improvement in maintaining a consistent indoor climate, which translated into energy savings and a more comfortable living environment, especially during the peak of summer and winter months.
Factors Influencing Attic Insulation Costs
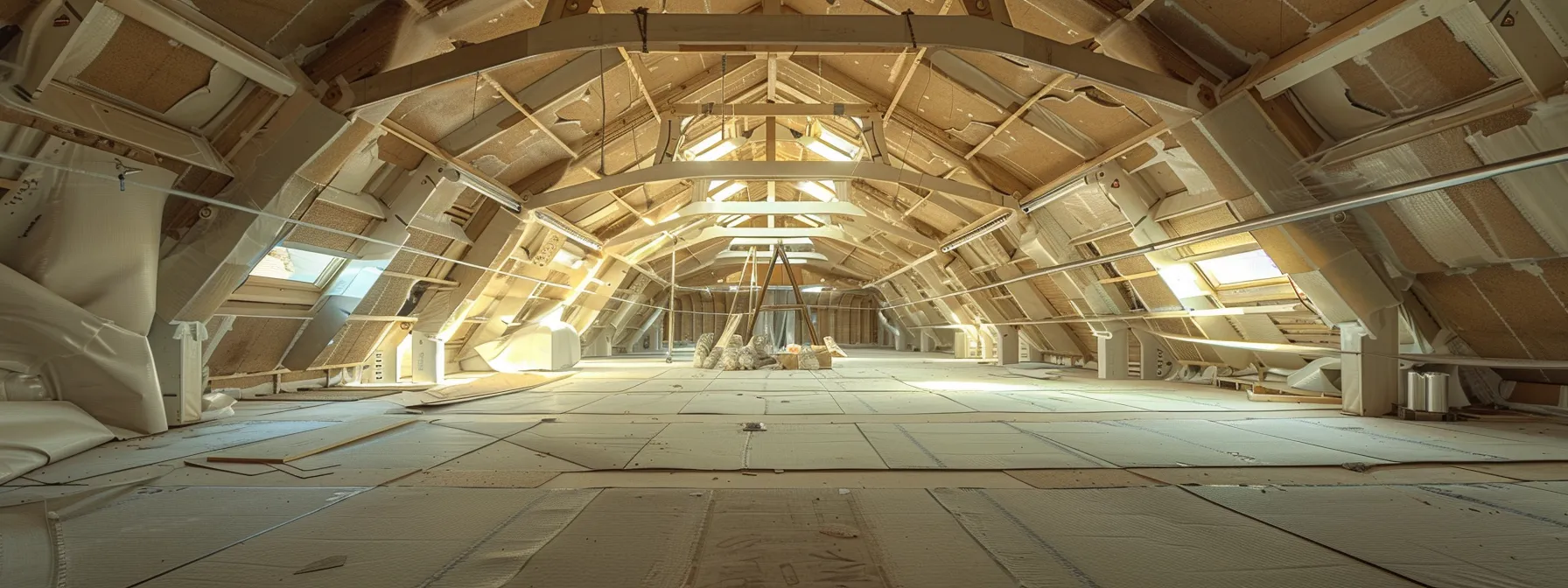
When I assess the cost of insulating an attic, several factors come into play. The size and design of your attic, particularly if it features a cathedral ceiling or complex trusses, can significantly influence the price. Accessibility and the difficulty of installation are also key considerations, as tight spaces may require specialized equipment or techniques. Regional climate plays a role too; homes in areas with heavy snowfall or high moisture levels may need more robust solutions. Additionally, the removal of old insulation and the rates charged by roofers for labor can affect the overall investment. Each of these elements will be explored in depth to provide a comprehensive understanding of attic insulation costs.
Size and Design of Your Attic
In my professional experience, the size and design of your attic are critical factors that can significantly influence insulation costs. For instance, a larger attic with a complex design, such as one with a cathedral ceiling, will require more materials and labor, which can increase the overall expense. Additionally, the specific climate of your region may necessitate a more robust insulation solution to effectively manage heat transfer and prevent water vapor from compromising the insulation’s effectiveness. Waterproofing
When I work with clients, I also consider the role of plastic vapor barriers in protecting against moisture intrusion, which is especially important in climates with high humidity. Properly installed vapor barriers can prevent water vapor from seeping into the insulation, thereby preserving its R-value and structural integrity. This attention to detail not only ensures a well-insulated attic but also contributes to the longevity and efficiency of the insulation material chosen, be it polyurethane spray foam or a traditional option.
Accessibility and Difficulty of Installation
In my experience, the ease of accessing your attic and the complexity of its layout can significantly affect installation costs for insulation. For example, a cramped attic with limited headroom can challenge the installation of traditional batts or blown-in materials, potentially increasing labor costs. Conversely, polyurethane insulation, while initially more costly, can be more straightforward to apply in hard-to-reach areas, potentially offsetting the higher material costs with reduced labor time.
I’ve also found that the unique features of an attic, such as irregular joist spacing or the presence of HVAC systems, can complicate the installation process. This is where the versatility of spray foam insulation shines, as it can conform to odd shapes and bypass obstacles with ease. However, for those with more accessible attics, traditional materials can be efficiently installed, offering a cost-effective solution that meets their building insulation needs without undue complexity.
Regional Climate Considerations
In my professional capacity, I’ve observed that regional climate is a pivotal factor when considering attic insulation costs. For instance, in areas with harsh winters, a higher R-value insulation like spray foam may be necessary to prevent heat loss, which could lead to increased upfront costs but substantial long-term savings on heating. Conversely, in milder climates, traditional materials such as fiberglass may suffice, offering a more cost-effective solution while still maintaining comfortable indoor temperatures.
Moreover, I’ve advised clients living in regions prone to high humidity that selecting the right insulation is crucial to prevent moisture-related issues. Spray foam‘s vapor barrier properties can mitigate the risk of mold and mildew, which is a common concern in such climates. This consideration not only impacts the health of the home’s occupants but also the durability and effectiveness of the insulation, influencing both the initial investment and the potential for energy savings over time.
Removal of Existing Insulation
In my professional practice, I’ve found that the removal of existing insulation is a critical step that can significantly impact the overall cost of attic upgrades. This process often involves labor-intensive work to clear out old, degraded materials, which can add to the project’s expense. Homeowners should factor in this removal cost when budgeting for new insulation, whether opting for high-efficiency spray foam or more traditional materials like fiberglass or cellulose.
Moreover, I’ve observed that the condition of the existing insulation can affect both the ease of removal and the subsequent preparation of the building insulation for new materials. For instance, insulation compromised by pests or moisture may require additional cleanup and repair, leading to increased costs. It’s essential for homeowners to consider these potential challenges when comparing the long-term value and upfront investment of different insulation options for their attic.
Contractor Rates and Labour Costs
In my dealings with various insulation projects, I’ve noted that contractor rates and labour costs can vary widely, often influenced by the complexity of the installation and the expertise required. For spray foam insulation, which necessitates precise application and specialized knowledge, labour costs can be higher. This is a critical consideration for homeowners, as the choice between spray foam and traditional materials like fiberglass or cellulose must account for these potential differences in installation expenses polyurethane.
From my experience, it’s evident that the duration of the project and the level of skill demanded can also affect labour costs. Traditional insulation may be more straightforward to install, potentially reducing labour charges. However, I always advise clients to seek quotes from reputable contractors who are experienced in attic insulation to ensure a fair price and quality workmanship, regardless of the material selected.
Evaluating Long-Term Savings and Return on Investment
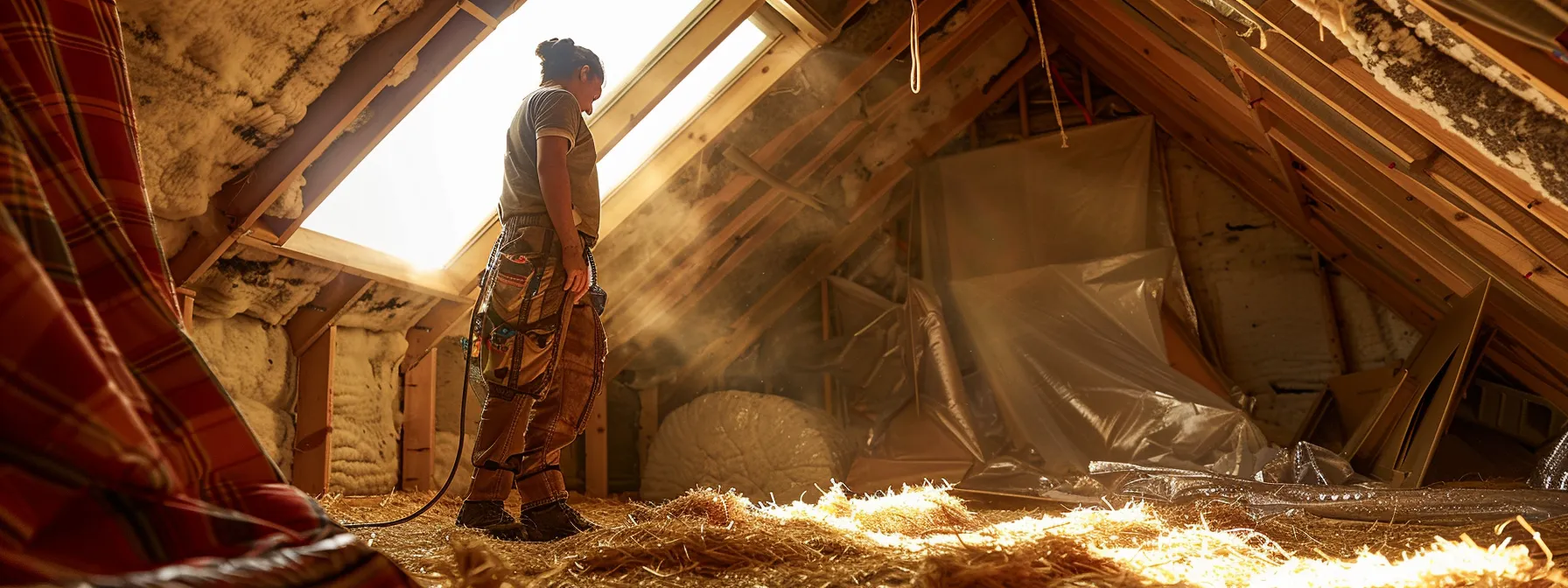
As we delve into the financial implications of attic insulation, I’ll guide you through the process of calculating energy conservation bill reductions and the impact on property value. We’ll explore available rebates and incentives, and compare the payback periods between spray foam and traditional insulation materials. Understanding these factors is crucial for assessing long-term savings and the return on investment, including the sustainability and environmental benefits of your choice.
Calculating Energy Bill Reductions
In my professional experience, calculating energy bill reductions following attic insulation upgrades can be quite revealing. Homeowners who choose spray foam often report a decrease in their heating and cooling expenses due to the material’s high R-value and airtight seal. This reduction is typically more pronounced than with traditional materials, as spray foam‘s ability to minimize air leaks leads to more efficient building insulation regulation and, consequently, lower energy consumption.
When I assist clients in estimating potential savings, we consider factors such as the size of the attic, the climate, and the existing heating and cooling systems. For example, in a cold climate, a well-insulated attic can significantly reduce the need for constant heating, leading to noticeable savings on energy bills. These savings, over time, contribute to the overall return on investment, making the initial cost of polyurethane spray foam insulation a financially sound decision for many homeowners.
Impact on Property Value
From my experience, investing in high-quality building insulation , such as spray foam, can significantly enhance a property’s market value. Prospective buyers often value the energy efficiency and cost savings associated with a well-insulated home, recognizing the long-term benefits of reduced utility bills and increased comfort. This improvement in energy performance can make a property more attractive in the competitive real estate market, potentially leading to a higher selling price.
I’ve seen firsthand how homeowners who opt for advanced insulation solutions like polyurethane foam can expect a favorable return on investment when it comes time to sell. The modern appeal of an energy-efficient home, coupled with the tangible benefits of a comfortable indoor climate, can be a compelling selling point. It’s clear that the right insulation choice not only saves on energy costs but also contributes to the overall value and desirability of a property.
Available Rebates and Incentives
In my professional capacity, I’ve guided numerous clients through the process of securing rebates and incentives for attic insulation upgrades. These financial incentives, offered by various government and utility programs, can significantly offset the initial costs of both polyurethane and traditional insulation materials. It’s essential for homeowners to research and apply for these programs, as they can make a substantial difference in the overall affordability of their insulation projects.
I’ve witnessed the positive impact that these rebates and incentives can have on a homeowner’s decision-making process. For example, a client was able to take advantage of a local energy conservation efficiency incentive program, which covered a portion of their spray foam insulation costs. This support not only made the project more feasible but also accelerated their return on investment, as they began to realize energy savings much sooner than anticipated.
Comparing Payback Periods Between Insulation Types
In my professional experience, the payback period for attic insulation varies significantly between spray foam and traditional materials like fiberglass or cellulose. Spray foam insulation, with its higher initial cost, typically has a longer payback period; however, its superior energy conservation efficiency can lead to more substantial savings over time. Homeowners should consider their long-term occupancy plans when evaluating these options, as the benefits of spray foam‘s higher R-value and airtight seal become more pronounced with each passing year.
traditional insulation materials often present a shorter payback period due to their lower upfront costs. While the
savings may not be as dramatic as with
the initial
is recouped more quickly, making it an attractive option for those with immediate
constraints. I’ve advised clients to assess their current
expenditures and insulation condition to determine the most
approach for their
Sustainability and Environmental Benefits
In my professional assessment, the sustainability and environmental benefits of building insulation insulation are not to be underestimated. Choosing materials like cellulose insulation, which is often composed of up to 85% recycled content, can significantly reduce the environmental impact of your home. This eco-conscious choice not only contributes to a reduction in landfill waste but also enhances the energy efficiency of your property, leading to long-term savings and a smaller carbon footprint.
Moreover, I’ve observed that homeowners who opt for spray foam insulation benefit from its durability and longevity, which means less frequent replacements and, consequently, less material waste over time. While the production of spray foam may involve chemicals, its ability to create an airtight seal can result in substantial energy savings, thus contributing to a more sustainable home environment. It’s a balance between immediate environmental impact and long-term energy conservation that I help my clients navigate.
Making the Right Insulation Choice for Your Home
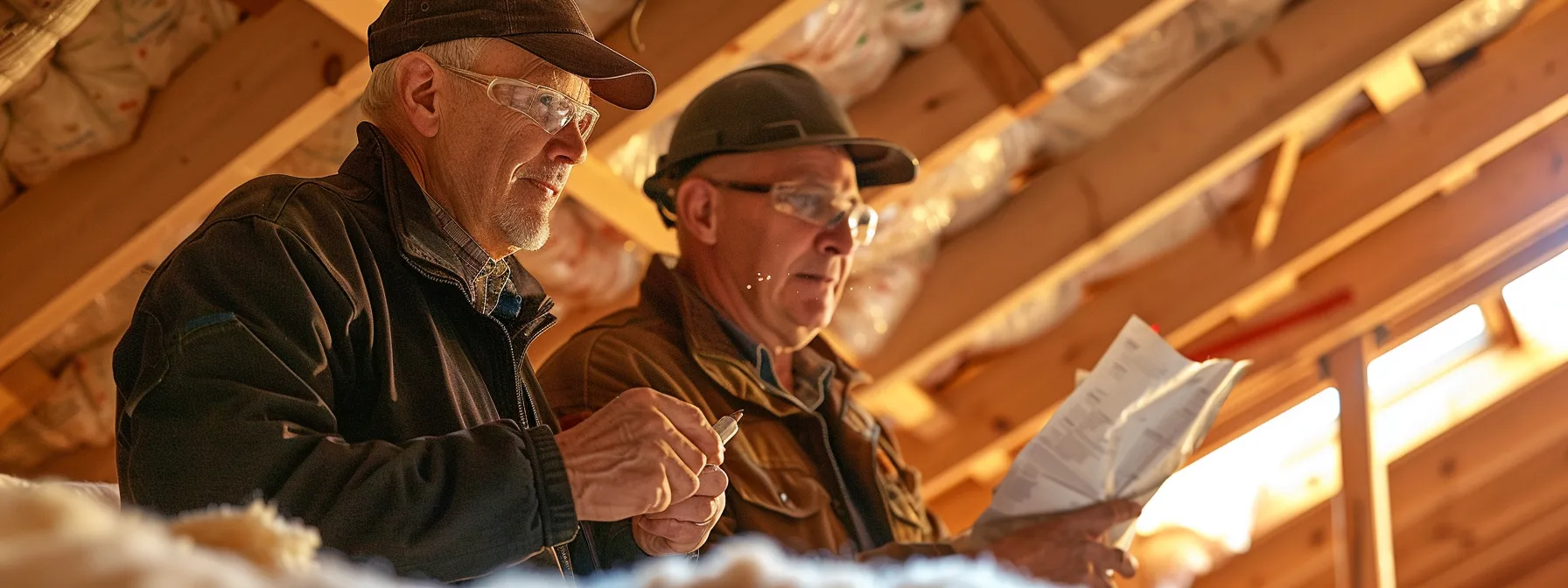
Choosing the right attic insulation involves a strategic approach to assessing your home’s specific needs and budgeting for both immediate and future financial implications. I’ll guide you through consulting with insulation experts to ensure your investment aligns with your home’s requirements. We’ll also examine the balance between upfront costs and potential long-term savings, culminating in well-informed recommendations tailored for homeowners. This section aims to equip you with the knowledge to make a decision that offers both immediate comfort and enduring value.
Assessing Your Home’s Insulation Needs
In my professional experience, assessing your home’s insulation needs is the first step towards achieving energy efficiency and cost savings. It’s essential to evaluate the current state of your attic insulation, considering factors such as age, existing damage, and any noticeable drafts or temperature inconsistencies. This initial assessment will inform whether spray foam, with its higher R-value and airtight seal, or traditional materials like fiberglass or cellulose, which are more budget-friendly, will best meet your specific requirements.
I’ve guided many homeowners through the process of identifying the most effective insulation for their homes. By examining the layout of your attic, the local climate, and your energy consumption patterns, I can help you understand the potential benefits of each insulation type. This tailored approach ensures that the choice you make not only fits your immediate budget but also aligns with your long-term financial and comfort goals.
Budgeting for Upfront Costs and Savings
In my role as a point of sales expert, I’ve advised numerous clients on the importance of accurately budgeting for both the upfront costs and the anticipated savings of attic insulation. It’s essential to consider the initial investment in materials like polyurethane , which may be higher due to its superior insulating properties and labor-intensive installation, against the long-term energy savings it can provide. This foresight into the cost-benefit analysis helps homeowners make informed decisions that align with their financial planning and energy efficiency goals.
Moreover, I’ve seen the financial benefits that come from choosing traditional insulation materials, such as fiberglass or cellulose, which offer a lower upfront cost. While the immediate savings are appealing, I guide my clients to also project the future energy costs associated with these materials, as they may not provide the same level of insulation as spray foam over time. By evaluating both the short-term and long-term financial implications, homeowners can select an insulation option that ensures a comfortable home and a healthy budget.
Consulting With Insulation Experts
In my professional journey, I’ve learned the importance of consulting with insulation experts when navigating the complexities of wall insulation. These specialists possess the knowledge to analyze your home’s unique structure and recommend the most cost-effective and energy-efficient insulation solution, be it spray foam with its high R-value or traditional materials like fiberglass. Their expertise ensures that your investment is tailored to your home’s specific needs, maximizing comfort and energy savings.
Engaging with an insulation expert can also provide clarity on the long-term benefits and potential savings associated with different insulation types. I’ve witnessed many homeowners gain peace of mind from these consultations, as experts can demystify the installation process and forecast the expected energy cost reductions. This guidance is invaluable in making an informed decision that aligns with both your immediate budget and your long-term financial goals.
Weighing Short-Term Costs Against Long-Term Benefits
In my professional dealings, I’ve learned that homeowners must balance the immediate financial outlay of attic insulation against the long-term energy conservation savings it can yield. While spray foam insulation presents a higher initial cost, its superior insulating properties and longevity can lead to significant reductions in heating and cooling expenses over time, making it a prudent investment for those planning to stay in their homes for the long haul.
Conversely, I’ve seen that traditional materials like fiberglass and cellulose offer a more modest upfront cost, which can be attractive for immediate budget considerations. However, it’s crucial to recognize that these options may result in higher energy costs in the long run, as they typically don’t provide the same level of airtightness and thermal resistance as spray foam, potentially necessitating additional building insulation upgrades or maintenance.
Final Recommendations for Homeowners
As a seasoned professional in the field of attic insulation, I recommend homeowners consider both the short-term and long-term financial implications of their insulation choices. If you’re planning to stay in your home for many years, investing in spray foam insulation could lead to greater energy conservation savings and a more comfortable living environment, despite the higher initial cost. It’s a decision that not only impacts your current comfort but also your future expenses and home’s value.
For those of you who are more budget-conscious or perhaps not planning to reside in your current home for an extended period, traditional materials like fiberglass or cellulose insulation may be the more prudent choice. These options offer lower upfront costs and can still provide significant improvements in energy efficiency. I’ve helped many clients navigate these decisions, ensuring they select the most cost-effective insulation that aligns with their specific needs and financial plans.
Conclusion
In assessing attic insulation, homeowners must weigh the higher upfront costs of spray foam against its superior energy conservation efficiency and long-term savings. Traditional materials like fiberglass and cellulose offer lower initial expenses but may lead to increased energy costs over time due to their lower R-values and airtightness. Consulting with insulation experts can provide tailored advice, ensuring investments align with individual needs and financial goals. Ultimately, the choice between spray foam and traditional insulation has significant implications for both immediate comfort and future financial returns.